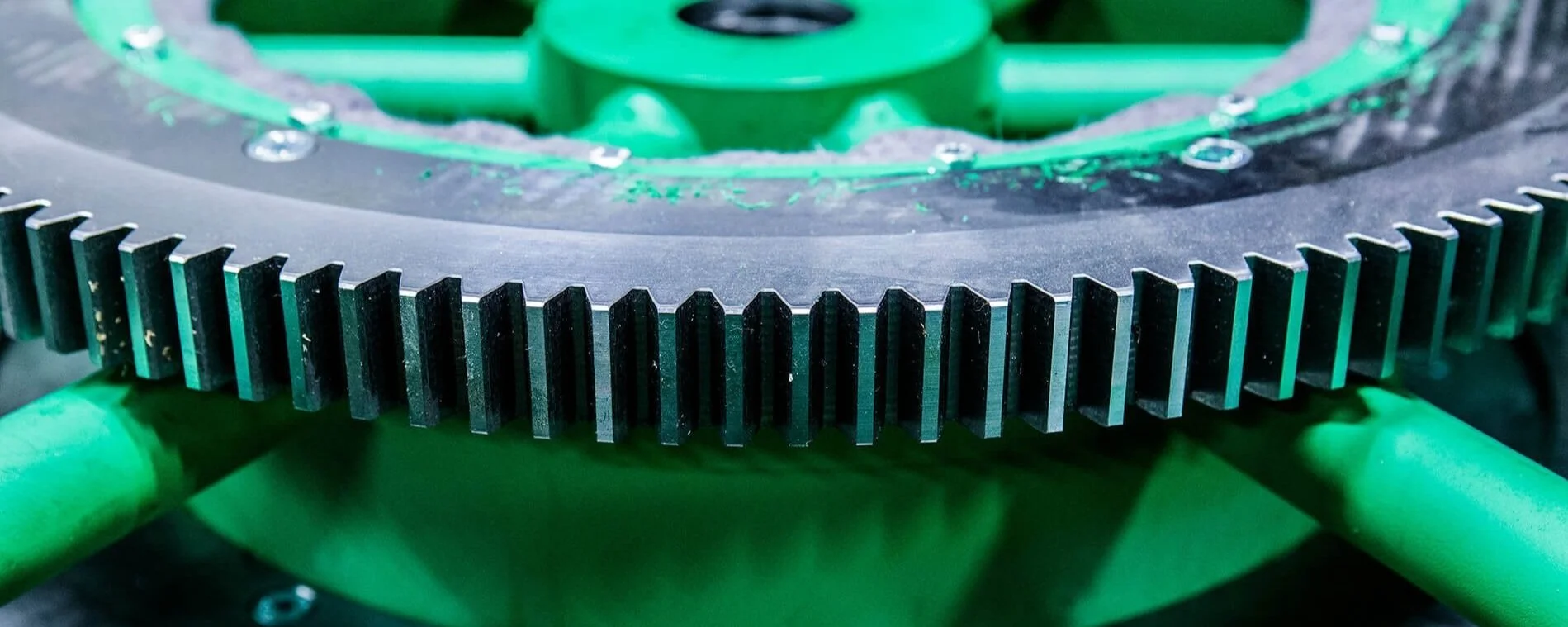
Service & spare parts
Unlock your business’s full potential
With our diverse range of service options tailored to your unique needs. Run your business with precision and watch it reach new heights with dedicated service agreements, specialist training, and genuine spare parts from Westrup.
Westrup offers a large variety of service opportunities to match your needs.
Contact service@westrup.com to learn more, or spares@westrup.com to order genuine spare parts for your Westrup and Norogard equipment.
ON-SITE TRAINING
In order to tailor the training specifically to your plant and taking into consideration your team’s knowledge, our service technician, along with your team, will thoroughly inspect your factory. Our aim is to provide on-site service to ensure your staff becomes acquainted with the specific machinery, allowing them to adjust parameters, valves, and handles, as well as promptly identify any potential malfunctions.
TEsT CENTER TRAINING
Our test centers provide a comprehensive range of training options for both products and equipment. By participating in our training programs, your employees will gain expertise in effectively setting up machinery and effectively controlling the product throughout the processing stages. This knowledge will enable them to make necessary adjustments that significantly enhance the overall quality of your end product.
SCHEDULED SERVICE AGREEMENT
By having a set agreement in place, your business can tailor the service arrangement according to its specific requirements. This may involve a combination of scheduled preventive services during convenient periods, predetermined rates, a defined level of emergency service, and even training sessions to keep your staff well-equipped with the necessary skills for handling your equipment.
EMERGENCY SERVICE
In the event of a breakdown, the initial action is to recognize and analyze the predicament at hand. Subsequently, a proficient service technician will be dispatched to your designated site equipped with the appropriate tools and essential equipment. Our service technicians promptly and diligently respond, ensuring a swift resumption of your production operations.
DIAGNOSTICS
A complimentary consultation is provided by a service engineer and a local sales manager from Westrup. They will visit your facility to carry out preventive maintenance on your machines. After a thorough assessment, a comprehensive proposal will be presented to you, detailing necessary adjustments and spare parts to prepare your plant for the upcoming seasons. Regardless of the age of your Westrup machines, diagnostic services are available for all.
More on Diagnostics
SPARE PARTS
Westrup have produced machines since 1958, and many machines are still in use to this day. All machines manufactured at Westrup have been catalogued making it possible to produce an original Westrup spare part specifically for your machine. This means that we are able to supply genuine spare parts for 99% of all Westrup machines produced over the past 66 years.
The original spare parts are the only spare parts that fully meet the requirements which are essential to reach a cost-effective operation of your plant. The spare parts will ensure the original quality of your machine, extend the lifespan, reduce downtime and lastly increase your operational stability.
Our distribution network has a wide range of spare parts available to you for immediate dispatch.
FAQ on Service & spare parts
-
Our aim is to provide on-site service to ensure your staff becomes acquainted with the specific machinery, allowing them to adjust parameters, valves, and handles, as well as promptly identify any potential malfunctions.
In order to tailor the training specifically to your plant and taking into consideration your team’s knowledge, our service technician, along with your team, will thoroughly inspect your factory.
-
Our test center provide a comprehensive range of training options for both products and equipment. By participating in our training programs, your employees will gain expertise in effectively setting up machinery and effectively controlling the product throughout the processing stages. This knowledge will enable them to make necessary adjustments that significantly enhance the overall quality of your end product.
Send an e-mail to your representative, or info@westrup.com, to book an appointment for training or testing in one of our test centers.
Our test centers are situated in:
Saint Melanie Sur Aubance, France
Sioux Falls, SD, USA
Slagelse, Denmark
-
By having a set agreement in place, your business can tailor the service arrangement according to its specific requirements. This may involve a combination of scheduled preventive services during convenient periods, predetermined rates, a defined level of emergency service, and even training sessions to keep your staff well-equipped with the necessary skills for handling your equipment.
-
In the event of a breakdown, the initial action is to recognize and analyze the predicament at hand. Subsequently, a proficient service technician will be dispatched to your designated site equipped with the appropriate tools and essential equipment. Our service technicians promptly and diligently respond, ensuring a swift resumption of your production operations.
To learn more contact: service@westrup.com
Need emergency service now? Call +45 31 25 20 36
-
A complimentary consultation is provided by a service engineer and a local sales manager from Westrup. They will visit your facility to carry out preventive maintenance on your machines. After a thorough assessment, a comprehensive proposal will be presented to you, detailing necessary adjustments and spare parts to prepare your plant for the upcoming seasons. Regardless of the age of your Westrup machines, diagnostic services are available for all.
Book diagnostic by sendin an e-mail to your representative, or info@westrup.com
-
To get your sample tested in our test centre, you need to provide the raw material. How much is needed depends on the product to be tested, how many processes are required and the types of machines that are used. Our in-house experts will guide you on this. During processing, we will uncover whether your ideal machine requires specific settings to give you the best result. After testing, you will receive a detailed report on how your crop was processed – which machines were used and a specification of how your product performed in each stage of the process. With this information, we will be able to provide you with the machine combination that is exactly right for your seed or grain.
Send an e-mail to your representative, or info@westrup.com, to book an appointment for training or testing in one of our test centers.
Our test centers are situated in:
Saint Melanie Sur Aubance, France
Sioux Falls, SD, USA
Slagels, Denmark
-
As a rule of thumb, we offer original geniune spare parts for 99% of all machines ever produces at Westrup. We manufacture the spare parts in our factory in Slagelse, Denmark, why we can ensure the correct measurements on close to every spare parts you may need.
-
When determaining the need for a spare part please contact: spares@westrup.com
-
We always recommend that you order Westrup spare parts, as that is the only way we can ensure your machines longevity.
When using genuine Westrup spare parts we ensure that they are specifically made for your machine type, we offer our expertise guidance and installation possibilities to ensure your down-time is kept to a minimum.
Contact: spares@westrup.com